Published 2024-07-05.
Time to read: 5 minutes.
Mini-Series
This article can be read standalone; however, is part of a mini-series that discusses how to increase the storage capacity and performance of the Ableton Push 3 Standalone (P3S). If you own a P3S, or are thinking of purchasing one, you might want to first read my review.
The articles in this mini-series are:
This article discusses some of the physics and a few of the electrical components for controlling temperature in a consumer electronics product.
Thermal Pads
A thermal pad is made from thermal interface material; its purpose in the article I wrote entitled Ableton Push 3 NVMe Replacement is to thermally connect the chips on the NVMe drive to a metal heat sink. Thermal pads are often baby blue; however, as shown in the above photographs, the P3S uses a pink thermal pad between the CPU module and the bottom plate, and, as we saw at the beginning of this article, another pink thermal pad between the external heat sink and the bottom plate.
Depending on the quality and conditions of use, a thermal pad can last anywhere from 5 to 10 years.
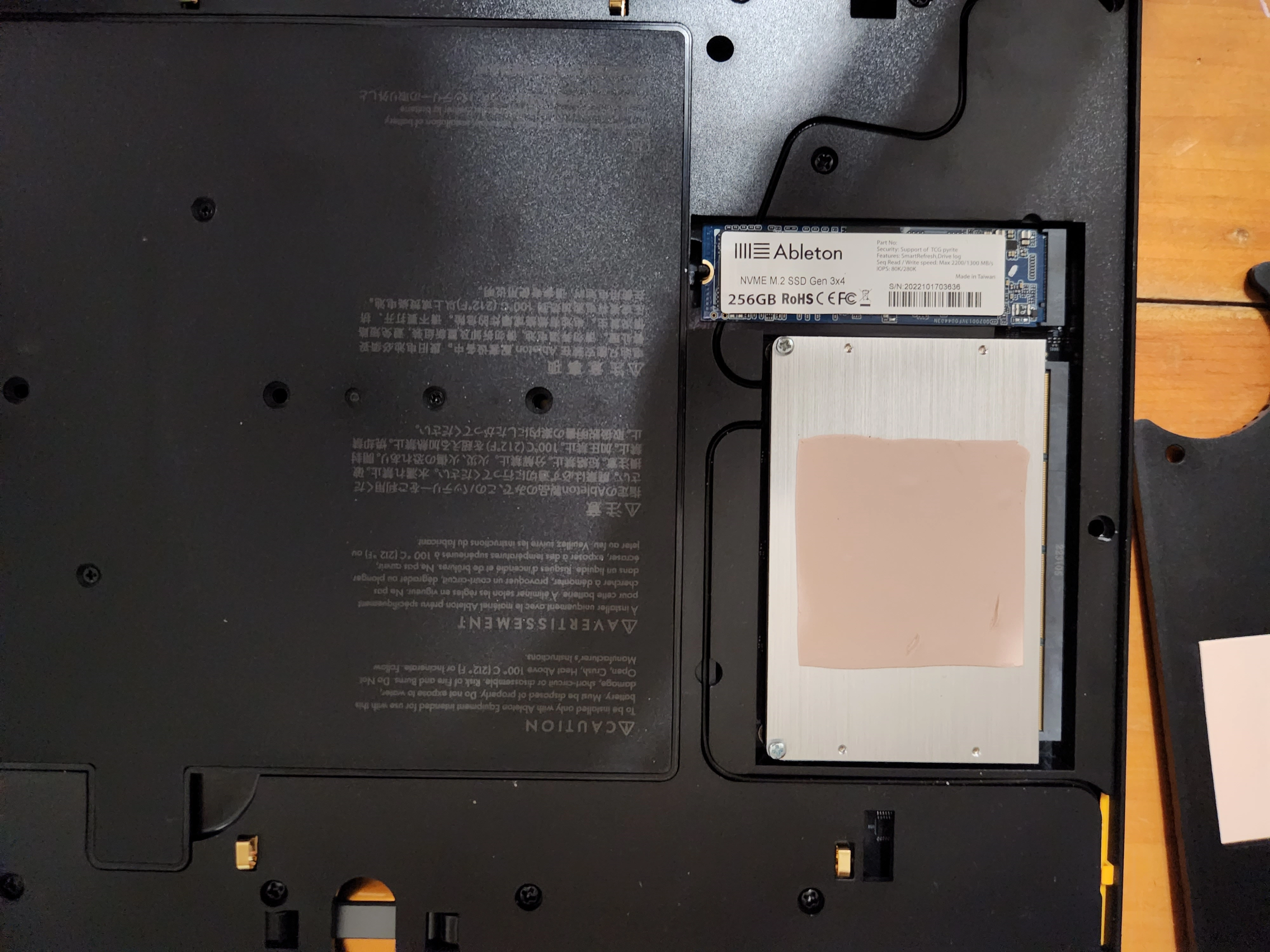
Folklore vs. Provable Facts
Some manufacturers state that thermal pads should not ever be reused, citing the introduction of air gaps and bubbles. Apparently reusing a thermal pad would cause the thermal pads to act more as an insulator than as a conductor. I do not have data that would indicate how well-founded the statement is. Someone should test this; the information source obviously has a profit motive.
Also from two manufacturers: When as thermal pad is removed, the surface should be cleaned with alcohol wipes and a microfiber cloth to ensure no traces are left behind. Again, I would like to see data on this.
Thermal Conductivity
Heat transfer only occurs 3 ways: via conduction, convection, and radiation. Of the three, conduction is by far the most effective.
Mode | Transfer Mechanism | Material |
---|---|---|
Conduction | Diffusion of electrons and phonon vibrations | Solids |
Convection | Density differences cause currents | Gases and liquids |
Radiation | Electromagnetic radiation | Non-opaque mediums |
This article focuses on conduction, because it is the dominant cooling mode for the P3S.
The thermal conductivity of a material characterizes its ability to transfer heat. For solids, thermal conductivity is due to the flow of free electrons, rather like how electricity is conducted. Materials with high thermal conductivity transfer heat faster than materials with low thermal conductivity. The thermal conductivity tells you the rate at which thermal energy is transported across a unit length of a material that has a unit temperature difference applied across that length.
Thermal conductivity in an electrical device depends upon:
- Density of material
- Pressure
- Temperature
- Temperature differential
- Material structure
In the SI unit system, thermal conductivity is measured in watts per meter per kelvin (W/mK). This defines the number of watts conducted per meter thickness of the material, per degree of temperature difference between the two surfaces.
The following table is ordered by increasing thermal conductivity, with thermal insulators at the top and the best thermal conductors at the bottom.
Material | Comment | Conductivity |
---|---|---|
Air | Effectively a thermal insulator. | 0.026 W/mK |
Powder coating | Used on computer chassis, and on the P3S bottom plate. Effectively a thermal insulator. | 0.174 W/mK |
Anodized aluminum coating | Used to coat the P3S heat sink underneath the P3S bottom plate. Anodizing means adding a layer of alumina to the aluminum surface. This thin layer of oxide is effectively a thermal insulator. Anodized aluminum has a higher surface area than unfinished aluminum and, therefore, radiates more infrared energy; however, radiation is orders of magnitude less effective than conduction for cooling. | 0.53-1.62 W/mK |
Marble | Used for kitchen table tops. | 2.8 W/mK |
Thermal paste | Commonly used between a CPU and its heatsink. Shelf life is 3 to 5 years, durability (working life) is 5 to 8 years. | 5 — 8 W/mK |
Thermal pads | Easily replaced |
3 — 16 W/mK The blue thermal silica gel pads that I purchased were rated at 6 W/mK. The pink thermal pads of the P3S might be rated at 14.5 W/mK. |
Low-carbon steel | Sheet metal, used for computer chassis, which might include the P3S bottom plate. Surface treatment, such as anodizing, generally reduces this value. | 34-54 W/mK |
Liquid metal paste (Conductonaut) | Can be highly dangerous for electronics and aluminum parts. | 73 W/mK |
Solid aluminum | Often used in heat sinks, for example underneath the P3S bottom plate. However, the P3S exterior heat sink is anodized, which greatly reduces its thermal conductivity. | 150-205 W/mK |
Solid copper | Used on motherboards | 357-413 W/mK |
Heat pipe | Used in a wide variety of electronics, including laptops and mobile devices | 4,000 to 100,000 W/mK |
Notice the huge disparity between the thermal conductivity of thermal pads, the metals and the coatings that the bottom of the P3S is constructed from. This tells us that although thermal pads are much better than simply relying on convection or radiation, thermal pads and the coatings greatly restrict the transfer of heat generated by the P3S electronics.
If a heat pipe was used effectively, the overheating problems of the P3S would completely go away. Furthermore, the heat pipe would allow more powerful and faster electrical components could be used.
Heat Pipes
Thermal pads, fans and heat pipes are commonly used in laptops for dissipating heat. Heat pipes do not require power, are very light, and provide extremely high heat flux — from 10x to 200x more than pure copper. Heat flux (also known as thermal flux, heat flux density, heat flow density and heat flow rate intensity) is the amount of heat energy passing through a surface, measured as the flow of energy per unit of area per unit of time. It is a vector quantity.
The following video by James Orgill of The Action Lab shows that heat pipes transfer heat energy dramatically faster than solid materials.
This video explains how heat pipesmic work in detail:
Perhaps Ableton might look at using a heat pipe in a future version of the P3S that features a more powerful CPU and larger NVMe drive.
Heat Sinks
Heat pipes can be combined with other components for heat transfer, such as extruded heat sinks, die-cast heat sinks, fin-stack heat sinks, and skived heat sinks. Heat transfer materials thermally bond the heat pipes to the heat sinks. This creates a thermal management system that can be individually tuned for each application.
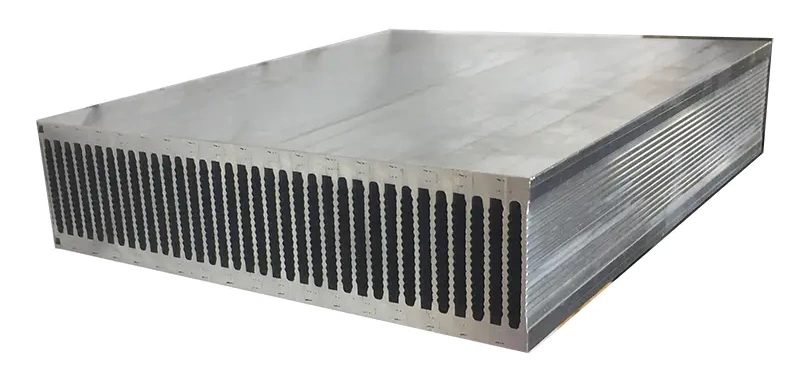
Vapor Chambers
Vapor chambers, also known as planar heat pipes, are relatively new. Tubular heat pipes act as heat dissipaters, while planar heat pipes act as heat spreaders.
Aftermarket Upgrade
I can imagine an aftermarket upgrade that would increase the height of a PS3 slightly, uses a heat pipe or vapor chamber for cooling, and has a variable-speed fan. This would support the biggest, fastest and hottest NVMe drive you can afford. I wonder if it might be possible to overclock the CPU if it was properly cooled?
Sources
- Metals, Metallic Elements and Alloys - Thermal Conductivities
- Kryonaut vs Conductonaut (Liquid Metal)
- Is Thermal Paste Necessary?
- Thermal conductivity of anodized aluminum oxide layer: The effect of electrolyte and temperature
The University of Cambridge has an online course which goes into the physics of conductivity: Introduction to thermal and electrical conductivity.
Mini-Series
This article can be read standalone; however, is part of a mini-series that discusses how to increase the storage capacity and performance of the Ableton Push 3 Standalone (P3S). If you own a P3S, or are thinking of purchasing one, you might want to first read my review.
The articles in this mini-series are: